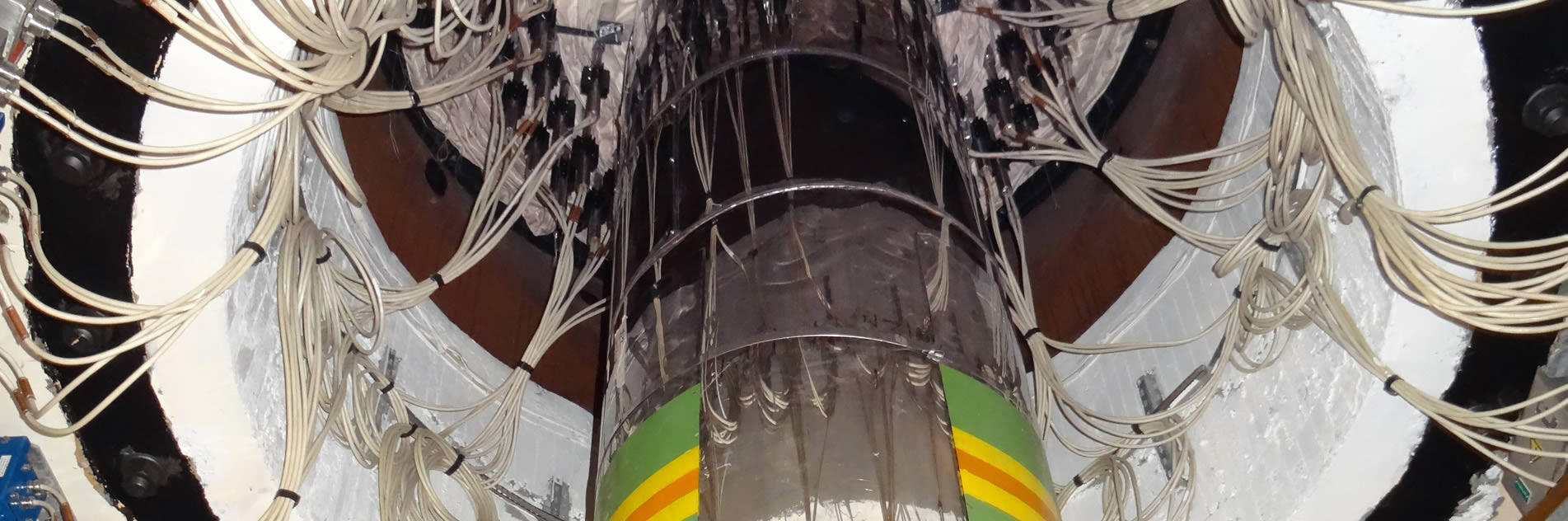
Thermocoax offers unique proprietary heating solutions to withstand extreme conditions of nuclear fission and fusion power plants.
Heating systems in nuclear environments need to perform optimally under extremes heat, mechanical and electrical stress. Thanks to our proprietary mineral insulated (MI) cabling, Thermocoax heating solutions meet all these requirements and function perfectly in this harsh environment. We also design custom systems when standard heating elements are not permitted.
Heating Systems for NPPs and Nuclear Experimental Loops
Thermocoax manufactures heating systems for fission or fusion reactors. In addition, we supply products for Nuclear Experimental loops, where conditions of radiation, temperature and pressure are reproduced.
Double barrier PRZ heaters with MI cable technology
Pressuriser heaters are essential in nuclear reactors to ensure that the primary coolant pressure remain high enough to prevent boiling on the fuel assemblies. . In 40 years, Thermocoax has supplied more than 10,000 PRZ heaters for new-build NPPs, retro-fit NPPs and test circuits. With a failure rate 3 times lower than conventional mechanisms, our double barrier design safeguards the pressure boundary of the vessel metallurgy by preventing IGSCC.
Thermocoax PRZ heaters have been developed using finite element analysis (FEA) to optimise the thermal, electrical and mechanical construction. Our heaters provide excellent heat conduction resulting in a long life time, demonstrated by operational experience. They are also available in various diameters and lengths and can be mounted vertically or horizontally.
- High watt density up to 40W/cm²
- Connectors up to 260°C, pressure tested up to 260 bars
- Designed according to international mechanical standards (ASME, KTA, RCC-M)
- 1E qualification available
Fuel pin simulators for experimental loops
Thermocoax fuel pin simulators are custom-made for the material characterisation and thermal studies that have to be performed on nuclear fuel pins.
And because we know that NPP manufacturers have their own fuel-specific configurations, dimensions, and assembly methods, Thermocoax solutions allow for simulating various fuel designs. The fuel pins are electrically isolated from the coolant, enabling experiments to reproduce core coolant circulation in steady state, transient and accident conditions.
The proprietary connectors on the simulators are designed to withstand voltage, current and temperature. Furthermore, thermocouples can be embedded at the client’s request.
- Outer sheath in Inconel and stainless steel
- Hot section length, 100 mm to 3000 mm
- Outer diameters, 4 mm to 22 mm
- Linear or cosine heat profile
Flexible Trace Heating Cabling for Easy Routing
Thermocoax trace heating solutions are designed to maintain temperature and keep process coolant fluid in fusion and fission reactors. We provide heating elements for pipes, tanks, plates, and high-density heating collars.
In critical PWR circuits, Thermocoax trace heating cables are deployed in Boron tanks to maintain temperature thus preventing crystallisation. They are also employed in fusion reactors (e.g. ITER), in vacuum chambers during the ‘baking’ phase to create the lowest possible vacuum.
Designed to withstand extreme radiation and function at high operating temperatures, our trace heating cabling is available in multiple configurations of line resistance, outer diameter and length. Our mineral insulated cabling comes with connectors to suit all conditions, and a tight bending radius for application in all design configurations.
- Waterproof and fireproof
- Inconel or stainless-steel outer sheath
- Competitive installation costs
Customised Ovens for R&D
Thermocoax ovens are manufactured on demand for R&D applications. In ‘swimming pool’ reactors, they are used for conducting material ageing experiments and heat tests. Because the heater is integrated with the overall assembly, thermal optimisation can be guaranteed. At the client’s request, we can also incorporate instrumentation such as RTDs and thermocouples. And thanks to our flexible cabling, Thermocoax ovens can be supplied in very small sizes, starting from a few centimetres.
- Temperatures up to 1100°C
- Dimensions from few cm to 1 m3
- No-weld in hot/cold transition
- Flexible cabling for easy routing
In-core Heating Systems
Thermocoax manufactures in-core heating systems small modular reactors (SMR), usually located in sparsely populated urban areas. In this type of reactor the heating elements are usually closer to the fissile materials.
Our heating systems are equipped with connectors designed for long-term tightness with state-of-the-art ceramic seals. Depending on the client’s needs, Thermocoax in-core systems are supplied for normal conditions or the extreme radiation, pressure and heat of a Design-Basis Accident.
- Small dimension, single or multiple contacts
- Contact pins in nickel or thermocouple material
- Qualified resin compound if permitted
- LOCA & post-LOCA resistant
Why use Thermocoax heating solutions?
Thermocoax MI cable technology for heating solutions is designed to withstand the harshest of conditions characteristic of the nuclear industry.
And when the standard solutions are not adequate, we pride ourselves on being able to provide customised heating solutions to individual client specifications. Our products are manufactured to match your expectations with regard to internationally accepted constructions standards.
Heating Solutions for NPPs : technical data
For further details about our high-grade heating solutions and related products, please do not hesitate to request a quote.